Extruded goods inspection vision system

To enhance quality control during extrusion processes, an extruded goods inspection vision system can be integrated. During extrusion, heated, plastically deformable and viscous masses such as plastics are forced through a shaping opening under pressure. The resulting extrudate can take on a variety of shapes, e.g. profiles, seals, pipes, etc.
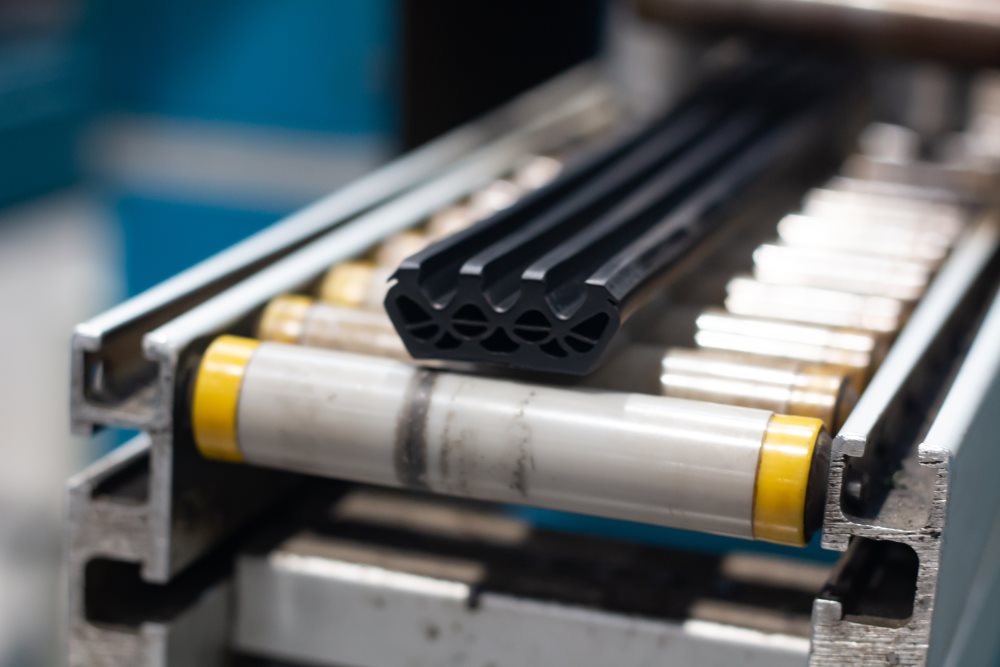
As the end product is manufactured continuously in this form of production, it is of fundamental importance for the process that deviations in the manufacturing tolerance or surface defects can be detected immediately, as otherwise there is a risk that the defect will continue over a very long period of the manufacturing process, leading to a high quantity of rejects and therefore to
high costs due to faulty production.
To reduce these costs and possible customer complaints, camera-based inspection systems are often used. Turnkey systems for extrusion applications are expensive and often have not been developed to meet the exact needs of the respective customers.
More and more companies are now developing their own inspection system for their specific application. To do this, you only 'invest' once in the development and then have a system that is perfectly tailored to your own needs, which can then be extended to other extrusion lines at a very low cost. In addition, you develop the know-how yourself within the company and are less dependent on external companies.
In this specific case, the customer produces plastic strips that are to be inspected for defects on both sides directly behind the extruder. In some cases, individual grains of the plastic granulate do not melt completely or impurities collect at the extruder's outlet nozzle, which then cause surface defects such as scratches, dents or similar. The aim of monitoring is to detect these defects as early as possible so that the process can be intervened in immediately and rejects can be reduced to a minimum.
Table of contents
Camera selection
First, we define the right industrial camera for the extruded goods inspection vision system application. Based on the customer's specifications, we recommended the following setup to the customer.
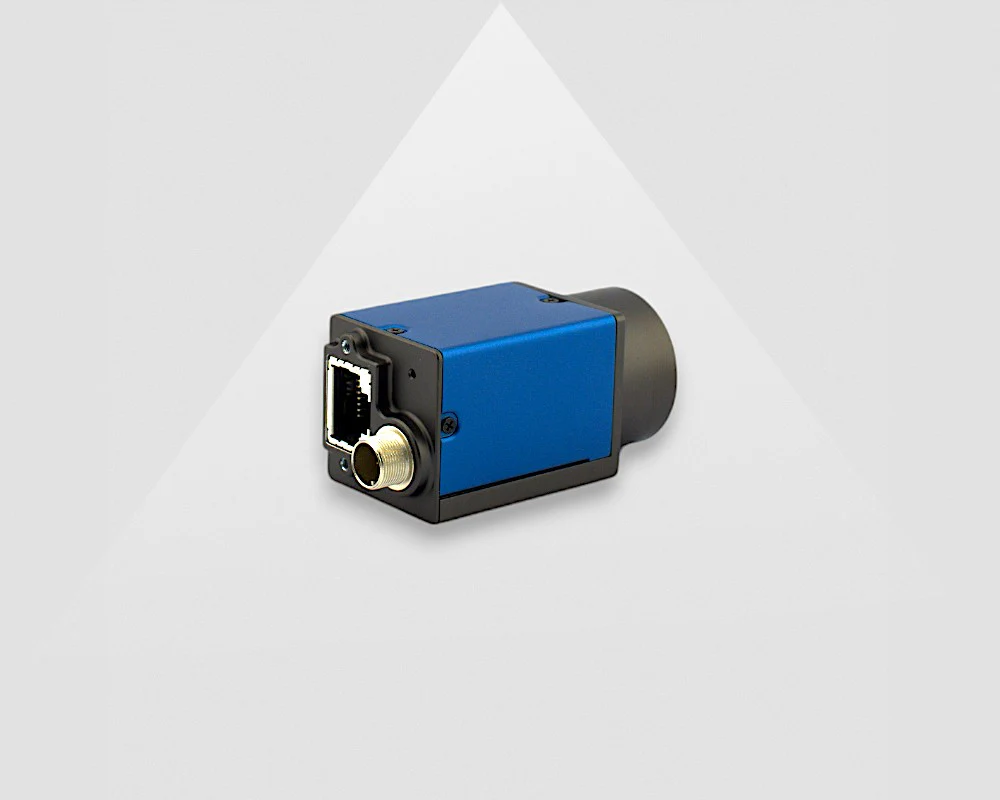
Key data:
- Maximum width of the strips: 80mm
- Extrusion speed: max. 5m/min
- Smallest error: 0.2mm
- Camera/PC distance: approx. 10 m.

Camera systems for image processing should be designed in such a way that the smallest detail of at least 3x3 pixels is displayed. With a FOV of 80x60mm, this means a resolution of at least 1200x900 pixels.
As the product moves during image acquisition, a global shutter camera should be used. You can find more information on the different shutter types of industrial cameras in our knowledge center here: Global shutter vs. Rolling shutter
According to the above calculation, the MER2-160-75GM-P camera would be sufficient. This is a global shutter Sony IMX273 with a 1/2.9' sensor with 1440x1080 pxl and a pixel size of 3.45µm.

Suitable lens for extruded goods inspection vision system
To determine the appropriate lens for this extruded goods inspection vision system application, we need to know the size of the image sensor used, the FOV to be covered and the working distance between the camera and the product to be inspected. The maximum possible working distance within the extrusion line is limited, both from the top and from the bottom of the product it is a maximum of 300mm.
Using the MER2-160-75GM-P in combination with a 16mm lens at a working distance of 300mm results in a FOV of 88x66mm. This C-mount lens is a good option for this application: VA-LCM-5MP-16MM-F1.4-015.

Lens calculator

Lighting for extruded goods inspection
The ideal lighting scenario depends on many factors, e.g. the surface condition of the product, ambient lighting, possibly changing light conditions depending on the time of year and day, etc. If the installation space allows, it is advisable to make the application independent of external light influences. This can be ensured by encapsulating the cameras and the lighting unit, for example. This measure ensures that the image quality achieved is always constant at any time of day or year. Especially if you use inspection software, this prevents the occurrence of possible pseudo errors.
The plastic skirtings have an anthracite-colored, only slightly reflective surface. Defects, inclusions as well as scratches or dents can always be reliably detected via a change in the surface texture of the strips.
For this extruded goods inspection vision system, it is therefore advisable to install light sources in addition to the camera setup, which make these superficial distortions stand out more clearly from the intact surface of the plastic strips. Our bar lights VA-BL3-119x16-W are a simple and cost-effective option for this, as they can be easily attached to existing structures using the optional brackets. To supply them with power, you can either use an existing 24V power supply in the extrusion line or you can use our VA-PS1-A1-60W-24V-1 Power Supply. If you want to connect several light sources to one power supply and also want them to be adjustable, you will find suitable options here: Powersupply for barlights.
Ideally, the lighting should be positioned at a fairly shallow angle of less than 45° to the product to be inspected, so that defects are clearly visible due to the reflection, which differs significantly from the original product. The matt surface in this application makes it somewhat easier to set up the lighting. In the case of highly reflective surfaces or surfaces with glossy effects, the use of polarizing filters can help. In any case, it must be ensured that there are no reflections caused by light hitting the lens directly. To prevent this, you can play with the positioning of the camera or light source on site to find the ideal setup for the application.
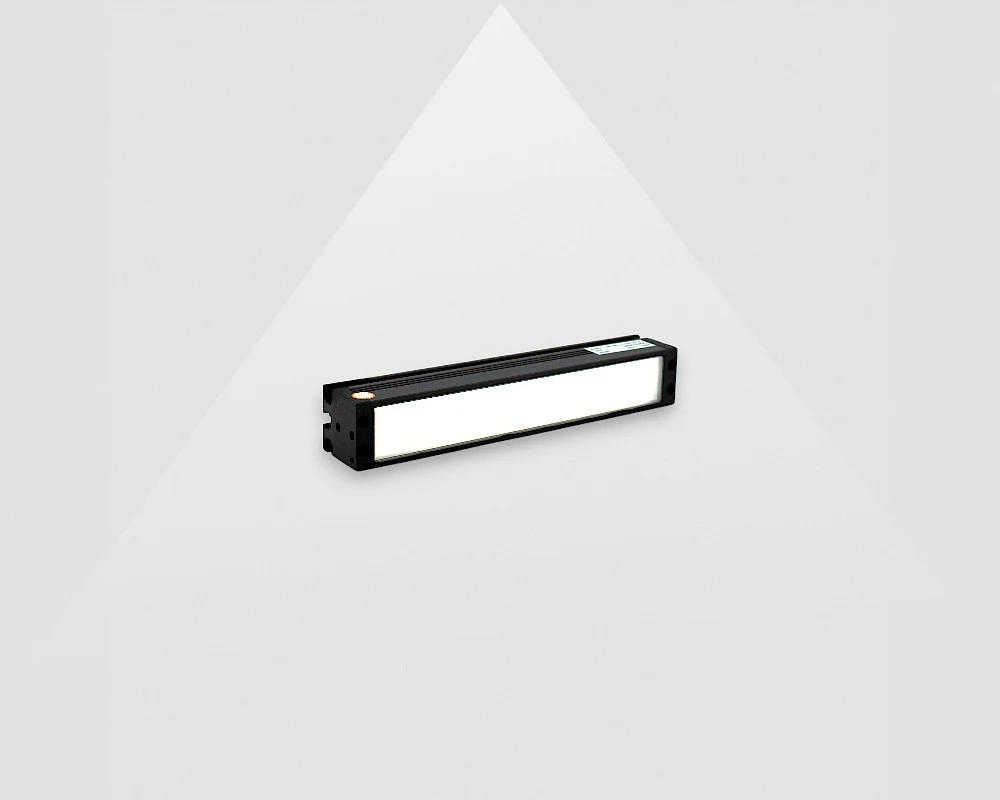
Image processing software
With the above setup, you can now view images on a PC and save them. This would be sufficient, for example, if the machine operator only needs to monitor the process from time to time by manually checking the images.
With this method, however, you will never achieve 100% control of the entire production, but at most random monitoring.
A few years ago, it was still very complex and extensive to use image processing software. This was not possible without programming knowledge. Thanks to the intuitive software solutions from Zebra Aurora Vision, this is now also possible for non-experts. The software is Windows-based and can be operated via drag & drop. All you need is a developer license and then a runtime license for each production line.
On our website you will find some videos that show the intuitive use and the possibilities of Zebra Aurora Vision software.
To get a first impression of this software solution, you can download the free lite version (Zebra Aurora Vision Studio 5 Lite) directly from our website.
If you would still like to use an integrator to help you get started with the software, we will be happy to help you with a recommendation for one of our integration partners.
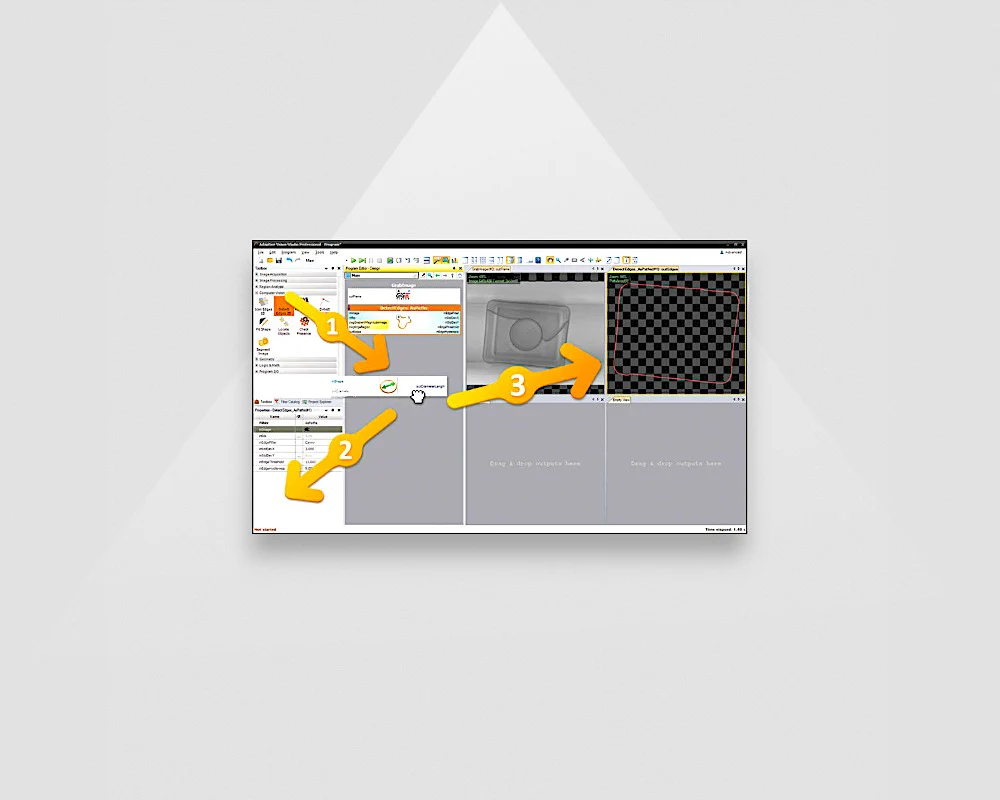
Support for extruded goods inspection vision system?
Would you like to have support from one of our machine vision experts for creating your own extruded goods inspection vision system? Or another similar vision system? Don’t hesitate to reach out by using the form below!