Quality control and Damage Detection in Car Inspection Tunnel

A car inspection tunnel is an area designed to visually inspect vehicles. The automotive manufactures use it for quality control and inspection purposes. Our machine vision cameras together with our computer vision software will capture images that then will be processed to examine the surface and detect any imperfections, defects or scratches.
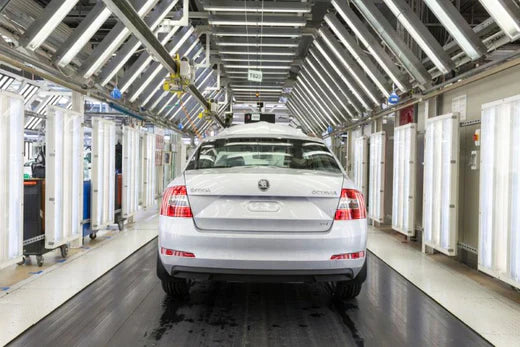
Car inspection tunnels can be used in the automotive manufacturing industry by vehicle manufactures as well as automotive suppliers. Use for quality control in vehicle assembly plans to perform inspections on new assembled vehicles before they leave the production line. Also utilized in the aftermarket industry, especially for damage detection, for car dealerships, body shops, refinishing facilities to first find the imperfections and then to ensure the quality of the work performed.
Table of contents
Machine vision camera selection for car inspection
The machine vision camera we selected for this car inspection project is our 20MP GigE Camera 'MER2-2000-6GM-P'. The engineer wanted to detect defects down to 1 millimeter in diameter on a non-moving vehicle. Since the details that we need to detect are very small, having a high-resolution industrial camera will give us the best results, in this case we are using a 20MP camera. Because the vehicle will be still while the pictures are taken, we are able to use a rolling shutter camera. We will be using a GigE camera because the distance between some of the cameras to the PC will be longer than 4.6 meters. We are also using a monochrome camera since they are three times more light sensitive than our color cameras.
We will be using a total of 48 cameras, 16 on each side of the box tunnel and another 8 on the ceiling. The car inspection tunnel box is 4 meters in height, 5 meters wide and 7 meters long. This is why we decided to go with so many cameras so each camera can focus on a smaller Field Of View giving us the most accurate answers. These many cameras will allow us to take pictures of every part of the vehicle from the tires to the top of the car. These many cameras will also allow us to capture pictures in different sized cars. The monochrome cameras, since they are more light sensitive, will allow us to detect tiny exterior imperfections all around the car such: scratches, dents, etc.
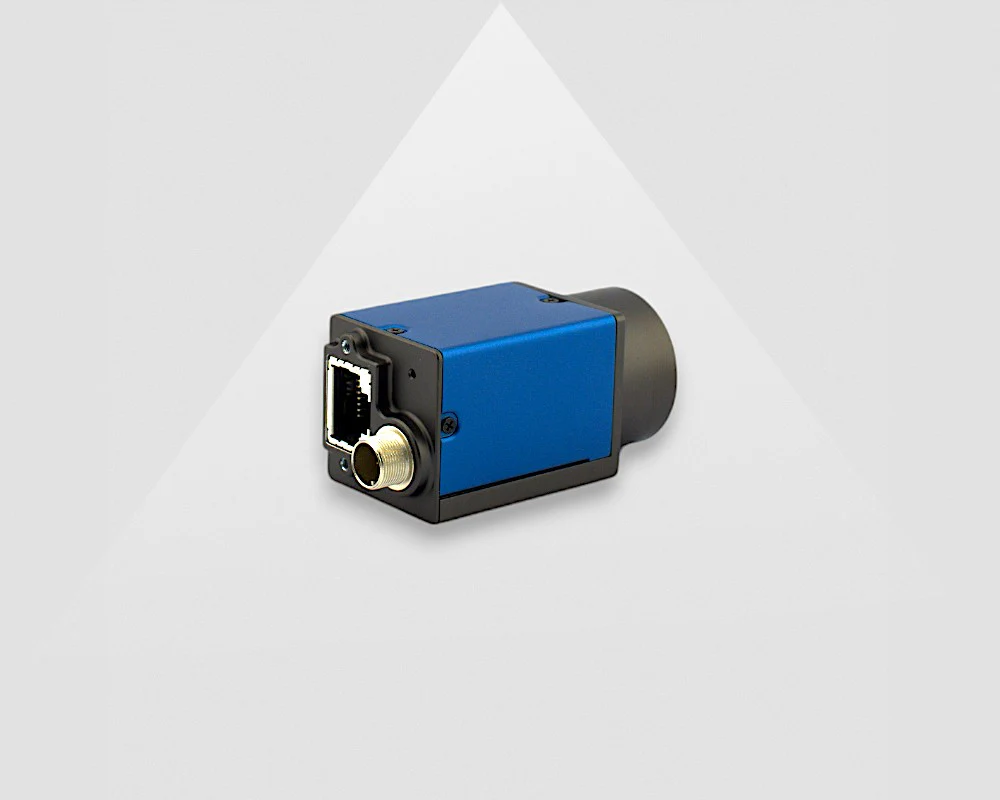
Industrial Lens for Sony IMX183 sensor
The selected camera for this car inspection tunnel has a Sony IMX183 sensor with a 1” sensor size. We will be using our lens calculator to select the best lenses for these cameras and solutions. To best calculate the lens, we need to know the horizontal Field of View (FOV) required and the working distance (WD). As I mention since we have a very large Field of View, we will be breaking down the FOV of each camera to 1750mmx1000mm. With a horizontal FOV of approximately 1750mm and a working distance of approximately 1600mm, we will get a FOV of 1746mmx1166 using our 25MP 12mm focal length 'VA-LCM-25MP 12MM-F2.4-120' lens. Calculations of the lens calculator have been attached below. The recommended focal length is 12mm lens, our suggested lens is a 25MP C-mount lens.
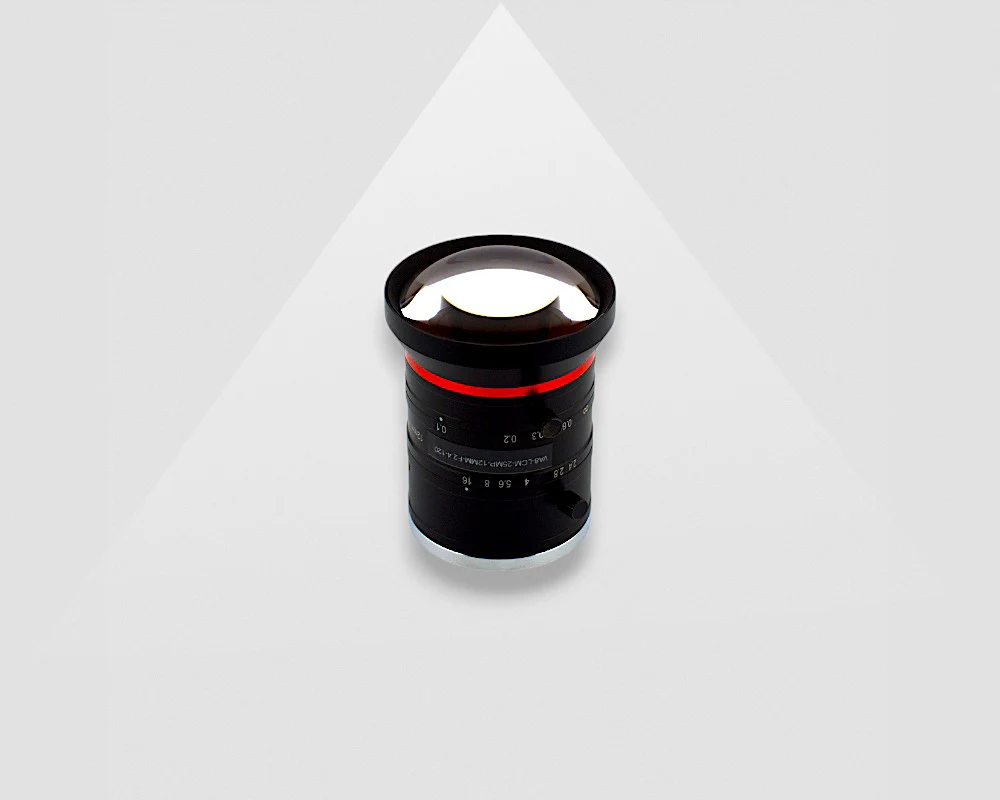
Lens Calculator
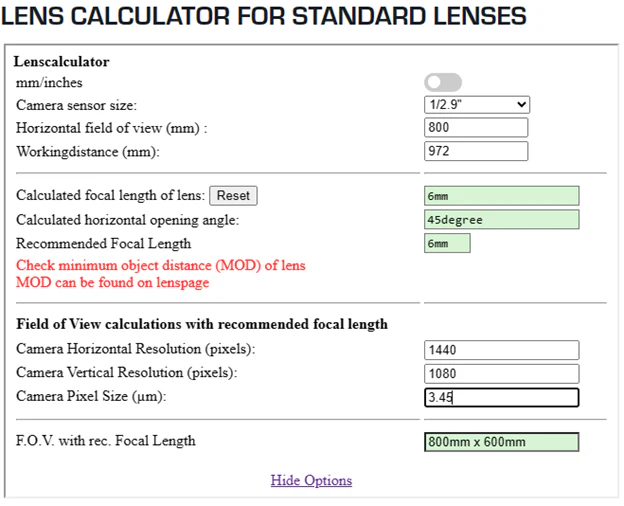
Car Inspection Tunnel Lightning Solutions
In all vision applications it is critical and very difficult to find lighting because of many different reasons such reflection, natural lighting, etc. Most of our customers that have similar car inspection tunnel applications use custom lighting, which we provide.
In this case, the engineer decided to go with our custom LED panel lights with well diffuse light. The metal in the car, the windows in the car, etc. can be very reflective. The engineer decided to use this reflection created by the car to capture the details needed.
Another very common lighting solution that our customers use and that they recommend using is the zebra effect on the LED panel lights. Another option can also be using polarized lights and adding polarizing filters to the lenses to get rid of any reflection that the car and lighting might
generate.
Every solution is very different, every set up is different so please contact us and we will be able to suggest the best lighting solution for your own project.
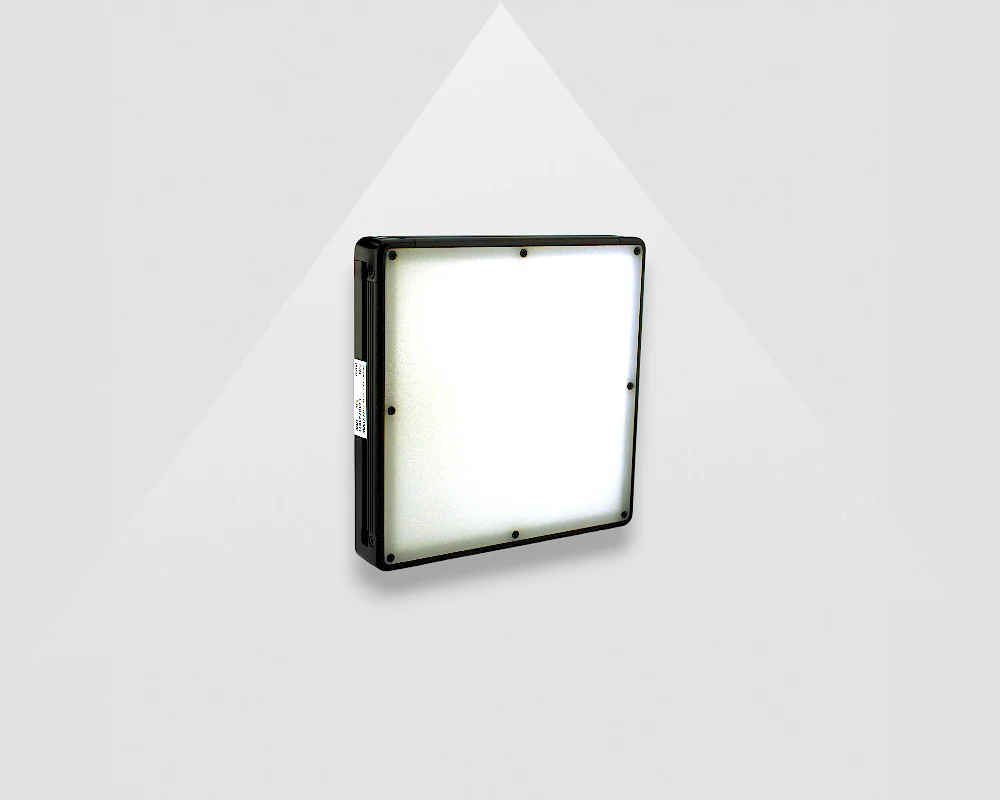
Image Processing software for Car Defect Detection
After we have found the best machine vision camera, lens and lighting solution for the automative defect detection application, we always suggest the customer to first find the best set up so then we can help them find the best software.
For this application, we suggested the Zebra Aurora Vision Studio 5. We suggested the engineer first download the lite version which is free, that way he can try the software and see if it works well with the application. The lite version would not work with live images, but an image can be taken and saved to try the program. If the trial version appears to be suitable after extensive testing, but final performance tests or special functions still need to be tried out, we are happy to make this possible. In these cases, we can also offer a 30-day trial version of the full program. With the Zebra Aurora, the engineer is going to be able to try the cameras, lenses and lighting by taking a picture and analyzing it in the software which then he will be able to flag any defects on the car inspection.
Zebra Aurora is a great option since it is made for vision engineers to create solutions without programming skills, it offers a variety of software packages depending on your specific needs. Our tech support team also offers quarterly training sessions for this software, and we are open to receiving pictures and documents to make free example programs.
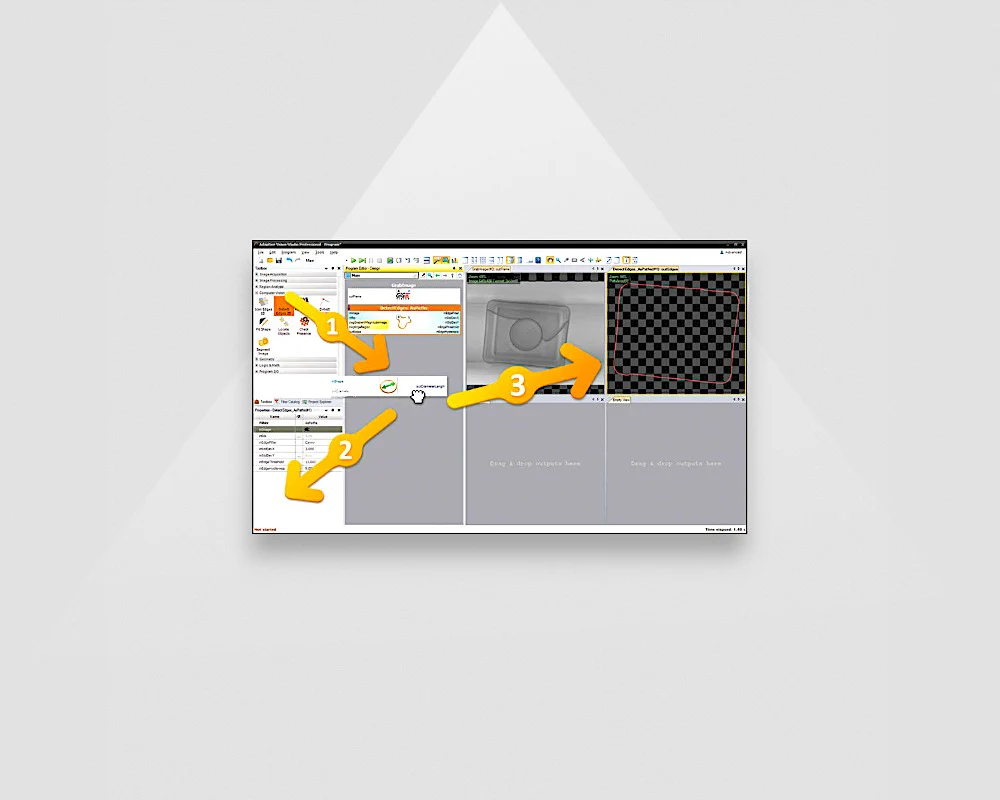
Support for Car Inspection Tunnel
We are aware that every project is different, your FOV could be larger or smaller, you might be dealing with natural light on top of reflection from the car, you might be unsure of what camera is needed or how many megapixels you need for the specific details that you need to detect within your picture. We at VA Imaging want to help you find the best machine vision components in car manufacturing such as camera, lens, lighting, software and any extra hardware needed for your application. Reach us out using the form below to get in contact with one of our account managers, which will gladly help you find the best solution for your car inspection project!