Bildverarbeitungskameras für Abfallsortierung und Recycling

Fortschrittliche Technologien wie die industrielle Bildverarbeitung spielen eine immer wichtigere Rolle bei der Verbesserung der Abfalltrennung und des Recyclings. Ein Bildverarbeitungssystem mit Bildverarbeitungskameras macht das Recycling schneller und genauer. Meistens werden diese Kameras über Förderbändern in Recyclinganlagen installiert. Während sich der Abfall über das Band bewegt, nehmen die Kameras hochwertige Bilder der Gegenstände auf. Mithilfe von Bildverarbeitungssoftware können die Bildverarbeitungskameras verschiedene Materialien wie Kunststoffe, Metalle und Papier schnell erkennen. Dieser automatisierte Prozess hilft bei der korrekten Sortierung der Abfälle, wodurch Fehler vermieden und Zeit und Geld gespart werden.

Table of contents
Einer der Kunden von VA Imaging bat um Hilfe bei der Auswahl einer geeigneten
Bildverarbeitungs-Kamera-Einrichtung für die Müllsortierung. Einer unserer Bildverarbeitungsexperten beriet das Recycling-Unternehmen bei der Auswahl eines kompletten Systems, das auf den Spezifikationen seiner Anwendung basiert. Dieser Artikel beschreibt in nur 5 Schritten, wie alle Bildverarbeitungskomponenten für das Müllsortier- und Recyclingsystem ausgewählt wurden. Möchten Sie eine persönliche Beratung für Ihre Anwendung erhalten? Teilen Sie uns einfach unten einige Spezifikationen Ihres Projekts mit und wir werden uns mit Ihnen in Verbindung setzen.
Kameraauswahl für ein Abfallsortiersystem
Die Beratung für die richtige Einrichtung für die Müllsortieranwendung beginnt mit der Auswahl einer geeigneten Bildverarbeitungskamera. Der Bildverarbeitungsexperte von VA Imaging empfahl den Einsatz unserer 16MP-Kamera 'ME2S-1610-24U3C' mit dem Sony IMX542-Sensor aufgrund der folgenden vom Kunden gewünschten Anforderungen.
Erstens wurde eine USB3-Schnittstelle als Kamerainterface empfohlen. Der Grund dafür war, dass der Kunde von der viermal höheren Bandbreite im Vergleich zu einer Gigabit Ethernet (GigE) Kamera profitieren konnte. Darüber hinaus wird die USB3-Schnittstelle für Anwendungen empfohlen, bei denen die Entfernung zwischen PC und Kamera aufgrund der begrenzten Kabellänge nicht mehr als 4,6 Meter beträgt. In der Anwendung des Kunden betrug diese Länge etwa 4 Meter. Außerdem mussten verschiedene Farben des Mülls erkannt werden. Aus diesem Grund wurde eine Farbkamera empfohlen.
Außerdem entschied man sich für den Einsatz einer Global-Verschluss-Kamera anstelle einer Roll-Verschluss-Kamera. Global-Verschluss-Kameras werden in Anwendungen eingesetzt, bei denen sich entweder die Kamera oder das Objekt bewegt, während das Bild aufgenommen wird. In diesem Fall bewegt sich das Förderband und hält während der Bildaufnahme nicht an. Eine Roll-Verschluss-Kamera, die sich hervorragend für stationäre Anwendungen eignet, ist für diesen Zweck nicht geeignet. Die Verwendung einer Roll-Verschluss-Kamera würde aufgrund der Bewegung zu einer starken Bildverzerrung führen. Alle Dosen, Flaschen und anderen Abfälle auf dem Förderband könnten „schief“ oder „gekippt“ erscheinen. Bei industriellen Anwendungen wie der Müllsortierung führt diese Verzerrung zu einer ungenauen Erkennung, da einige Abfälle nicht so erscheinen, wie sie tatsächlich sind. Eine Global-Verschluss-Kamera verhindert diese Fehler, indem sie realistische, unverzerrte Bilder aufnimmt. Weitere Informationen zum Global Verschluss vs. Rollenden Verschluss finden Sie in diesem Artikel in unserem Wissenszentrum.
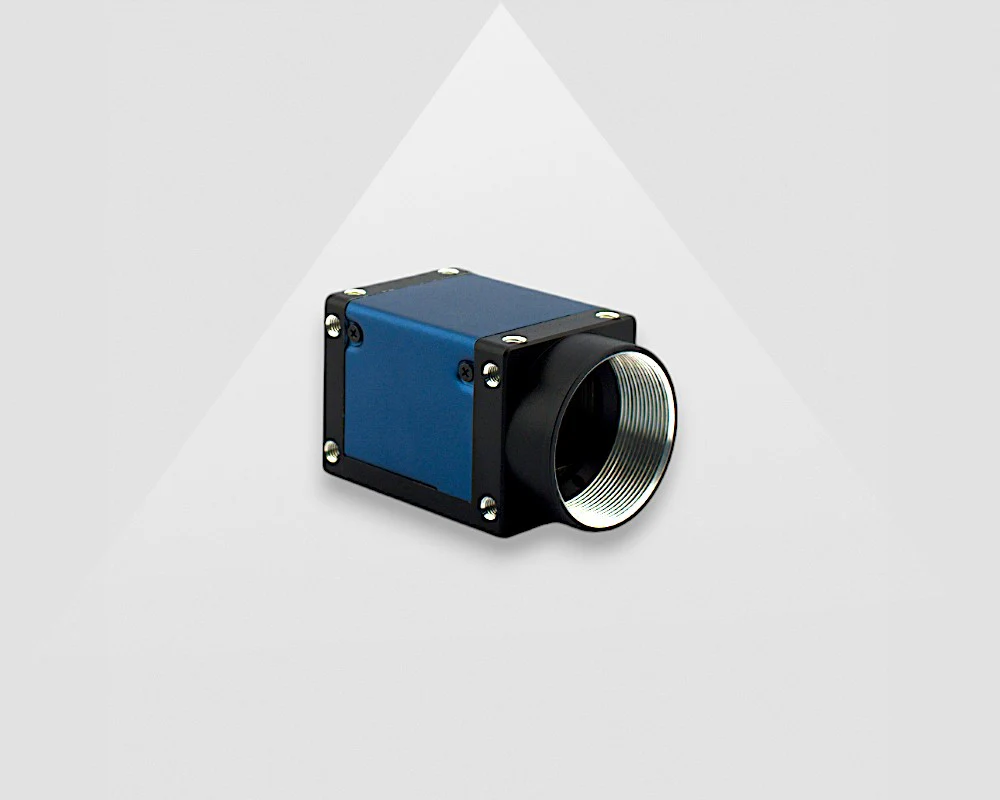
Der Kunde wusste nicht, welche Auflösung erforderlich war, um die verschiedenen Arten von Müll zu erkennen. Deshalb bot unser Bildverarbeitungsexperte an, bei der Berechnung auf der Grundlage von zwei Spezifikationen zu helfen: das erforderliche Sichtfeld (FOV) in mm und die Systemauflösung (mm/Pixel). Das Förderband, auf dem sich der Müll bewegt, hat eine Breite von 425 mm, die dargestellt werden sollte. Die Höhe war nicht wichtig. Es wurde eine Systemauflösung von mindestens 0,1 mm/Pixel gefordert.
Auf der Grundlage dieser Informationen musste eine Bildverarbeitungskamera mit einer Breite von mindestens 4250 Pixeln ausgewählt werden. Unsere 16-MP-Kamera erwies sich als eine hervorragende Lösung. Diese Kamera hat 5320x3032 Pixel, was zu einer Systemauflösung von 0,08 mm/Pixel führt. Die Berechnung ist in Abbildung 1 dargestellt, die Auflösungsberechnung wurde in Microsoft Excel erstellt.
Zusammenfassend lässt sich sagen, dass diese 16MP-Farbkamera mit dem IMX542-Sensor eine erschwingliche Bildverarbeitungskameralösung für die Abfallsortierung und das Recycling darstellt, die von der hohen Auflösung und Lichtempfindlichkeit profitiert.

Auswahl des Objektivs für die IMX542-Kamera
Damit die 16-MP-Vision-Kamera funktioniert, wählte der Vision-Experte von VA Imaging ein geeignetes C-Mount-Objektiv für die Kamera aus. Das richtige Objektiv mit der richtigen Brennweite wurde vom Vision-Experten auf der Grundlage von zwei weiteren Spezifikationen berechnet: dem Sichtfeld (FOV) in mm und dem Arbeitsabstand in mm. Der Arbeitsabstand ist der Abstand zwischen dem Objekt und der Kamera. Darüber hinaus ist es wichtig, ein Objektiv zu wählen, das für die Sensorgröße der 16-MP-Kamera geeignet ist. Die 16-MP-Sensor-Kamera hat eine Bildsensorgröße von 1,1“, der Sony IMX542
Um das am besten geeignete C-Mount-Objektiv für diese Bildverarbeitungskamera zu berechnen, bietet VA Imaging ein eigenes Online-Tool zur Berechnung von Objektiven an. Auf der Grundlage der Kameraauflösung, des erforderlichen Sichtfelds und des Arbeitsabstands konnte die Brennweite berechnet werden. Der Kunde gab an, dass er mindestens 425 mm Breite bei einem Arbeitsabstand zwischen 950 und 1350 mm sehen wollte.
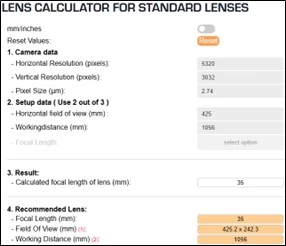
Unser 35MM-C-Mount-Objektiv 'VA-LCM-25MP-35MM-F2.4-120' erwies sich als ein großartiges Objektiv für die 16MP-Kamera. Die Verwendung unseres 35MM-Objektivs bei einem Arbeitsabstand von etwa 1056mm ergibt ein Sichtfeld von 425x242mm. Dies ist in Abbildung 2, der Brennweitenberechnung des Objektivs, dargestellt.
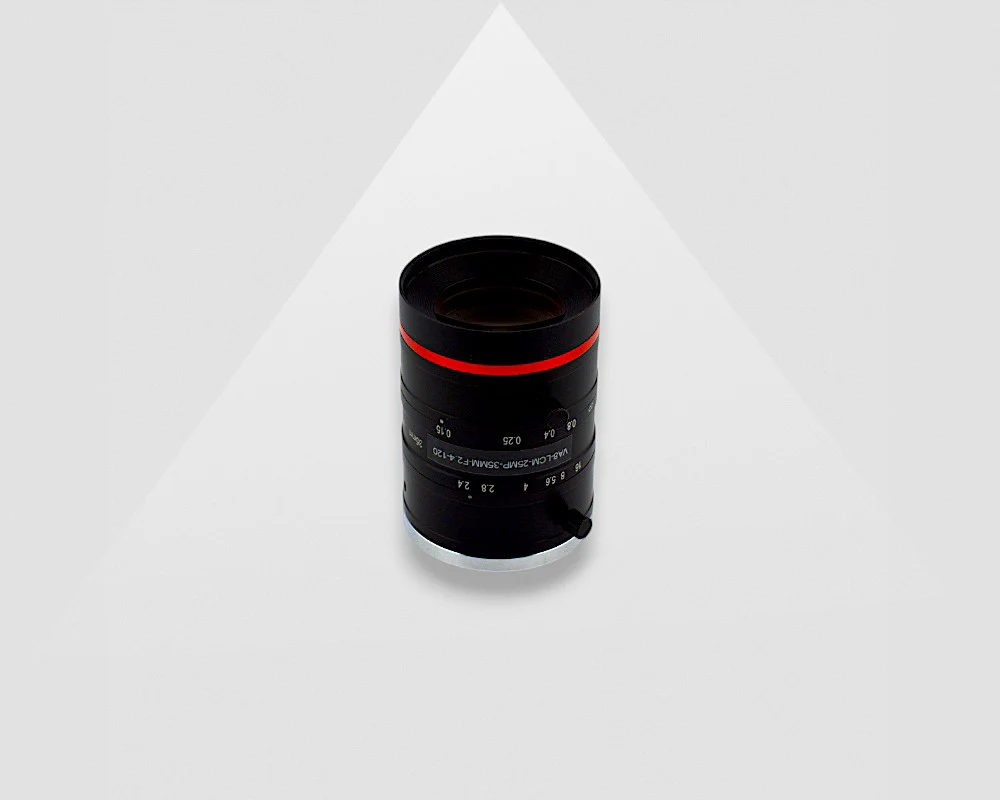
Zubehör für Abfallsortiersysteme
Bildverarbeitungskameras, wie die 16-MP-Kamera, sollten an einen PC angeschlossen werden. Um eine stabile Verbindung zwischen diesem PC und der Bildverarbeitungskamera zu gewährleisten, empfahl der Bildverarbeitungsexperte die Verwendung eines USB3-Kabels von VA Imaging. Für dieses Bildverarbeitungssystem zur Abfallsortierung wurde unser 4,6 Meter langes USB3-Kabel empfohlen, da die Länge zwischen dem PC des Kunden und der Kamera 4 Meter beträgt.
Darüber hinaus wurde unsere Stativhalterung für diese IMX542-Sensorkamera vom Vison-Experten für eine einfache Integration des Abfallerkennungssystems ausgewählt.
Maschinelle Beleuchtung für die Abfallerkennung
Es wird dringend empfohlen, einem Bildverarbeitungssystem wie dieser Abfallsortierungsanwendung eine Beleuchtung für maschinelles Sehen hinzuzufügen. Der Kunde teilte dem Bildverarbeitungsexperten von VA Imaging mit, dass die Fabrikumgebung, in der das System aufgestellt werden soll, nicht gut beleuchtet sei. Deshalb wurde beschlossen, eine abgeschlossene Box um das Förderband zu stellen, in der der Abfall erkannt wird.

Bildverarbeitungssoftware zur Abfallerkennung
Dieser spezielle Kunde hatte noch keine Erfahrung mit der Auswahl von Hardware für ein visuelles Müllsortiersystem. Sein Unternehmen hatte jedoch viel Erfahrung mit dem Schreiben und Implementieren von Software. Für diese spezielle maschinelle Bildverarbeitungsanwendung zur Müllsortierung zog der Kunde es vor, seine eigene Software in Python zu schreiben. Er entschied sich, unser kostenloses SDK für Beispielprogramme zu Rate zu ziehen, einschließlich des Python-Beispiels zum Aufnehmen von Bildern. In einem der Artikel in unserem Wissenszentrum finden Sie weitere Informationen zur Verwendung eines Python-Beispiels mit PyCharm.
Für die anfängliche Programmierung wurde unser kostenloses Software Entwicklungskit (SEK) verwendet, um Bilder aufzunehmen und zu speichern und die Kameraparameter für die Müllsortierung einzustellen. Das SEK unterstützt Betriebssysteme wie Windows, Linux und Android und ist mit normalen und industriellen PCs und ARM-Plattformen kompatibel. Das SEK unterstützt Programmiersprachen wie C++, C#/.NET und für dieses Bildverarbeitungssystem: Python.
Unterstützung für Machine-Vision-Anwendungen
Möchten Sie von einem unserer Bildverarbeitungsexperten Unterstützung bei der besten Bildverarbeitungslösung für die Müllsortierung erhalten? Oder bei einer anderen ähnlichen Recycling- oder Müllanwendung? Zögern Sie nicht, uns über das Formular unter diesem Link zu kontaktieren: Unterstützung für Bildverarbeitungsanwendungen.